What is Lean Production and How is it Applied?
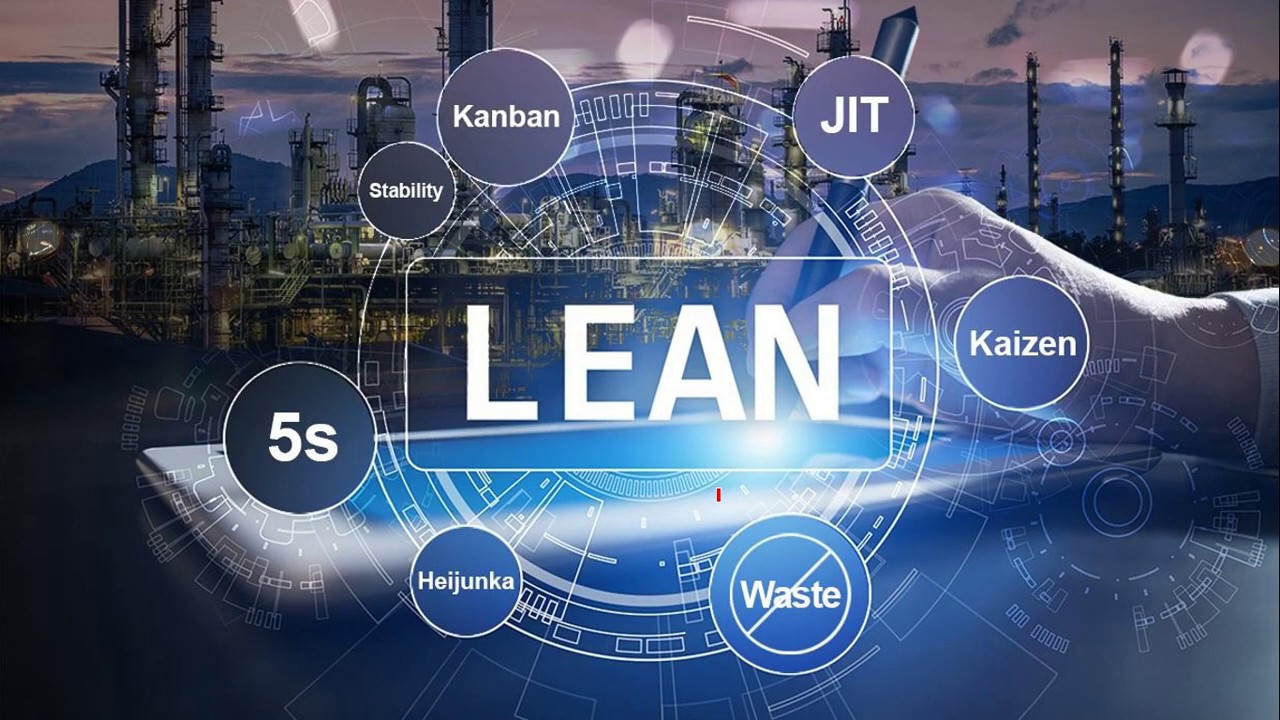
In today’s competitive business world, businesses need to adopt various methods and approaches to increase their productivity and reduce their costs. One of these approaches is Lean production. Lean manufacturing is a production philosophy that aims to minimize waste and maximize value-creating activities.
What is Lean Production?
Lean manufacturing is a production system whose main objective is to increase efficiency by reducing waste. This approach was developed by the Japanese automaker Toyota and has been adopted in many industries worldwide. Lean manufacturing aims to continuously improve processes to meet customer demands in the most efficient way. This philosophy involves identifying value-creating activities and eliminating all elements that are considered wasteful.
In Lean manufacturing, seven basic types of waste have been identified: overproduction, waiting, unnecessary transportation, over-processing, inventory, movement and defects. These types of waste reduce efficiency in the production process and increase costs. Lean production aims to eliminate all activities that do not create value for the customer by minimizing these types of waste.
Lean Production Principles
Lean production is based on five basic principles. These principles enable production processes to be managed more efficiently and effectively. The first principle is the definition of value. Value is determined by the customer and only activities that create value for the customer are considered in this context. The second principle is mapping the value stream. The value stream includes all the stages the product goes through in its transformation process from raw material to final product. This mapping helps to identify and eliminate waste. The third principle is to create uninterrupted flow.
This principle aims to minimize interruptions and waiting times in production processes. The fourth principle is the pull system. This system ensures that production is based on customer demand and prevents overproduction. The fifth and final principle is perfection. Lean manufacturing involves continuous improvement and the pursuit of excellence.
How is Lean Production Implemented?
The implementation of Lean manufacturing starts with analyzing the current state of the business. This analysis helps to identify waste and identify value-creating activities. The implementation of Lean manufacturing is often carried out in conjunction with the Kaizen (continuous improvement) philosophy. The first step is the creation of a value stream map. This map helps to identify waste in existing processes and plan how to improve the value stream.
A value stream map is a visual representation of the entire production process and shows where waste occurs. The second step is the implementation of the 5S methodology.5S consists of the initials of five words of Japanese origin: Seiri (sorting), Seiton (organizing), Seiso (cleaning), Seiketsu (standardizing) and Shitsuke (discipline). 5S is a methodology for organizing the workplace and keeping it clean, making production processes more efficient. The third step is the implementation of the Kanban system. Kanban is a pull system that allows production processes to be organized according to demand. This system ensures that stock levels are kept under control in production processes and unnecessary production is prevented. The fourth step is the implementation of continuous improvement (Kaizen) processes. Kaizen aims to continuously improve production processes by making small and continuous improvements. This process involves employee involvement and suggestions and enables the business to continuously become more efficient.
Lean Production Techniques and Tools
Lean manufacturing is implemented using a variety of techniques and tools. These techniques and tools help to make production processes more efficient and effective. One of these is the Value Stream Mapping (VSM) technique. The VSM is a visual representation of existing processes and identifies where waste occurs. This mapping helps to plan how to improve processes. Another technique is the 5S methodology. 5S is a methodology for organizing the workplace and keeping it clean, making production processes more efficient.
The Kanban system is also an important Lean production tool. Kanban is a pull system that allows production processes to be organized according to demand. This system ensures that stock levels are kept under control and unnecessary production is avoided. In addition, continuous improvement (Kaizen) processes are also an important part of Lean manufacturing. Kaizen aims to continuously improve production processes by making small and continuous improvements. This process involves employee involvement and suggestions and enables the business to continuously become more efficient.
Benefits of Lean Production
Lean manufacturing brings many benefits to businesses. These benefits include reducing waste, increasing efficiency, lowering costs and improving customer satisfaction. Lean production minimizes waste and makes production processes more efficient. This helps to reduce costs and increase profit margins. Furthermore, Lean manufacturing aims at continuous improvement of production processes. This increases the competitive advantage of the business and expands its market share.
Lean production increases customer satisfaction. Responding quickly and efficiently to customer demands increases customer satisfaction and loyalty. In addition, Lean manufacturing improves the environmental sustainability of the business. Reducing waste minimizes environmental impacts and helps the business to fulfill its environmental responsibilities.
Lean Manufacturing and Continuous Improvement
Lean production is closely linked to the philosophy of continuous improvement (Kaizen). Kaizen means “change for the better” in Japanese and refers to the process of continuous improvement. Lean manufacturing aims to continuously improve production processes and encourages employee participation in this process. Kaizen increases the efficiency of the business and reduces waste by making small and continuous improvements. This process includes suggestions and feedback from employees and enables the business to continuously improve. Lean production and Kaizen should be a philosophy embedded in the culture of the business. This should be adopted and consistently applied at all levels of the business. In this way, the business continuously becomes more efficient and increases its competitive advantage.
Lean production is a production philosophy that aims to increase efficiency by reducing waste. This approach maximizes value-creating activities and aims to meet customer demands in the most efficient way. Lean manufacturing is based on five core principles: defining value, mapping the value stream, creating a continuous flow, pull system and excellence. The implementation of Lean manufacturing is achieved by analyzing existing processes, applying the 5S methodology, using the Kanban system and adopting continuous improvement processes. Lean manufacturing brings many benefits to businesses: reducing waste, increasing efficiency, lowering costs and improving customer satisfaction. These benefits increase the competitive advantage of businesses and support sustainable growth. Lean manufacturing is tightly linked to the philosophy of continuous improvement and should be adopted at all levels of the business. Thanks to this, the business continuously becomes more efficient and expands its market share. Lean manufacturing is critical for businesses that want to succeed in today’s competitive business world.
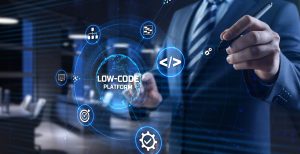
Previous Post
What is Low Code and What are its Advantages?
Next Post
What is Six Sigma and How is it Applied?
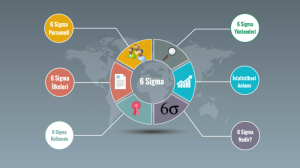